Typically, industries are pretty resilient to disruptions – even big ones. For example, when a large earthquake in eastern Japan caused a nationwide drug shortage on March 11, 2011. General panic followed as doctors and patients scrambled to ensure they could get a hold of prescriptions on which people rely – but that supply chain rebounded in less than six months, thanks to fast repair of damaged factories, importation from foreign countries, and a quick ramp-up of production in existing factories. The impact of other significant disruptions, be they human-made or “acts of God,” are similar. Even in the case of the Suez Canal incident, the only time in living memory when a shipping barge managed to command global attention and spur so many memes, the media coverage may well outlast the impact: once the ship went on its merry way, international trade will likely only see ripple effects into mid-May. All told, that’s decent resilience.
SUEZ, EGYPT – MARCH 29: People watch as the container ship ‘Ever Given’ is refloated, unblocking the … [+]
Getty Images
But the impact that COVID has had on the manufacturing industry seems much more acute – we’re seeing in real-time, and at an incredibly rapid clip, an evolution that would otherwise have taken years or even decades to occur if it was instead left to the “invisible hand of the market” to push forward. In the last year, the pandemic has pulled into incredibly sharp focus the various cracks in how we approach manufacturing and supply chains. As a result, suddenly, the entire industry is wide-awake.
For the first time in the decades since Industry 4.0 became a talking point, it’s now becoming real – and there are a handful of opportunities ripe for the taking as we move into a post-pandemic era:
Transparency in the Supply Chain
A lack of insight into supply chain data – fewer eyeballs on factory floors to manually track and account for inventory, along with shipping delays and product shortages – highlights the need for more transparency, which requires digitization in the supply chain process. Those who were able to turn to already-established AI-driven prediction engines and machine-vision powdered inventory systems quickly noticed trends on the demand side and reassessed output. And those without a digital eye on their supply chain were left scrambling.
But issues of changing consumer demand, shipping delays, and a diminishing workforce aren’t unique to the pandemic; they were skewed to their extreme. The technological solutions that gave manufacturers a leg up in “unprecedented times” can help everyone involved in a given supply chain efficiently and quickly understand the various levers that need to be pulled to respond to even a minor disruption. With more data, more transparency, and more automation in the supply chain, vendors, purveyors, and consumers all stand to benefit.
Distributed Production
A significant contributor to the various disruptions we saw in 2020 (and beyond) in manufacturing, in particular, are due to the industry’s outsized reliance on China and the all-in bet manufacturers have made on lean and just-in-time manufacturing. What we learned during not just the pandemic but during the Suez blockage as well is that the distance between the consumer and the component manufacturer matters; it’s a force multiplier. Expediting parts from one U.S. city vs. another as a workaround to support a U.S. consumer is a manageable problem compared to meeting that same need from Asia.
We achieve with distributed production a world in which a disruption in one geography doesn’t have crippling effects on the rest of the world – again, good for everyone involved, especially with the looming threat of ongoing trade wars and tariffs. Manufacturers that build where they sell will realize lower distribution costs, faster times to market, reduced working capital, reduced friction from government policies, and overall increased resiliency.
Less Reliance on Manual Labor
Social distancing on factory floors and a workforce diminished by active COVID infections exacerbated the issues manufacturers already face when it comes to manual labor: high turnover, low satisfaction, and costs that scale as production scales. While there’s the perception that automation has displaced the workforce, this is far from reality (and no such doomsday is looming on the horizon, with the World Economic Forum predicting that as many as 133 million new roles may emerge as companies embrace automation and uncover new opportunities for humans to work alongside machines). What is very real is that the continued reliance on manual labor to perform tedious, repetitive tasks throughout production cost manufacturers big over the last year and will continue to do so – unless they actively embrace automation and the opportunity to reskill the workforce.
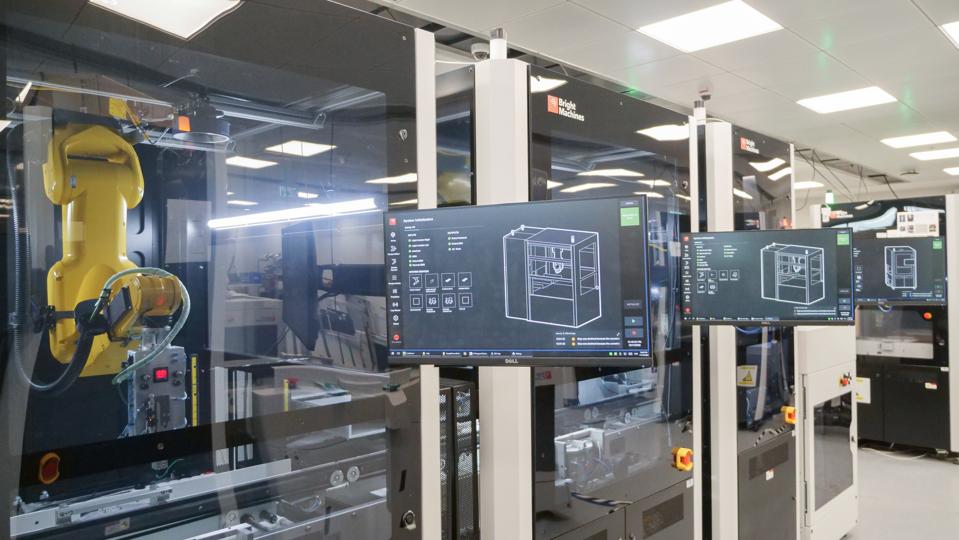
Microfactories automate product assembly and inspection
Bright Machines
Increased Speed of Innovation
During the early days of the pandemic, we saw just how inflexible most factories are – while a few were able to switch up their lines to help produce the PPE that the medical profession desperately needed, most were left to issue placating statements about solidarity because their lines are designed to make one specific product, and changeovers are expensive and slow as molasses. With the speed at which consumer desires change and the speed at which designers and innovators are ideating on new products, this glacial pace is borderline unacceptable. The opportunity now, with this shortcoming brought to the forefront of manufacturers’ minds, is to ensure that factories are as flexible and dynamic as innovation itself. Automation is key to this, but not the inflexible custom-built hardware solutions of decades past – software-defined solutions that enable fast changeover will be essential to seizing the opportunity to keep up with the speed of innovation.
Again, all of these opportunities ripe for the taking – point to a future for the manufacturing industry that’s digitized and decentralized. On this front, the pandemic has merely succeeded in speeding up the inevitable. The payoff will be huge: we’ll see more data-driven decision-making thanks to insights and transparency, while more flexible, dynamic automation that pairs hardware with software will allow for distributed, potentially reshored production, with the added benefit of solving for longstanding labor issues. The result: an industry that is by design more resilient in the face of future disruptions and operating at a higher caliber even in times of normalcy.